Environmental dredging, the process where contaminated sediment under water is removed, treated, and/or placed in a new location, is often necessary because sediments around cities and industrial areas are frequently contaminated with a variety of pollutants; however, projects can easily become complicated when debris is present within the dredging footprint. Guidelines and resources for identifying debris do not provide definitive guidance for managing debris and minimizing their impact on the 5Rs of environmental dredging (Removal, Resuspension, Release, Residuals, and Risk). A paper presented at the 2022 Western Dredging Association (WEDA) National Conference and Exposition, Managing Debris for Environmental Dredging Projects (Beaver et al.), synthesizes available resources on debris considerations to provide a common basis for identifying and evaluating debris issues for environmental dredging projects. Below is EA’s webinar on the topic followed by a summary.
Types of Debris and Key Characteristics
Experience has shown that debris in waterways and waterbodies include a myriad of items, some uniquely local and others more common. These include but are not limited to trees and logs, concrete slabs, piles, cable wires, vehicles, miscellaneous metal objects, and in some cases unexploded ordnance. The authors developed a matrix of commonly encountered debris items and categorized them by the key characteristics listed below:
- Size—Physical dimensions of debris determine dredgability and handling needs. Long objects prevent bucket closure for mechanical dredging, and these and other bulky objects can prevent access to targeted sediments underneath.
- Embeddedness—Since large objects may require removal prior to dredging, their embeddedness in sediment is a key factor in their impact on operations.
- Material Hardness and Density—Materials such as rotted wood may be soft enough that debris shear and clog machinery during the dredging process, while harder debris can cause problems even at small sizes by preventing bucket or cutterhead penetration into sediment, causing wear in transport pipes, and jamming pumps. Materials that are light or buoyant may become dislodged, adding to logistics necessary to manage floating debris.
- Debris Distribution—Concentrated debris pockets or zones (“dense debris”), as compared to widely distributed debris throughout the dredging footprint, often have differing logistics for removal even for the same material type.
- Environmental Concerns—Some debris may be a source of pollutant release or contain chemicals that require special handling or disposal based on the regulatory framework.
Debris Impacts on Dredging Operations
Debris can significantly impact the effectiveness, implementability, and cost of environmental dredging projects. It can interfere with dredge operations by impeding removal equipment’s efficiency with penetration, movement, and sediment capture, often requiring multiple removal attempts targeting the same mass of sediment. Unfortunately, dredging equipment is typically not designed for debris removal and may take several attempts to sufficiently move the debris, or dredging operations may need to be paused for a secondary attachment to be installed for the removal equipment. Multiple dredging attempts, in turn, reduce efficiency, and the disturbed sediment becomes lower density or even fluid-like, which exacerbates impacts associated with the 5Rs of environmental dredging. The figures below illustrate the difficulties associated with a single mechanical dredging bucket or hydraulic cutterhead’s interaction with debris within the sediment bed.
A summary of the debris impacts on resuspension, contaminant release, and post-dredging residuals is provided in the table below.
Debris Identification Methods
The authors emphasize the importance of debris investigations in order to better define expected debris and, in turn, reduce the risk of occurrence and having to address unexpected debris. Quantifying approximate locations, sizes, and characteristics of debris leads to cost-savings for many projects by allowing the development of efficient logistics for debris removal, management, and disposal. The majority of investigative technologies typically used only map the surface of the sediment; however, the authors stressed the importance of finding and incorporating new technology capable of extending into the subsurface given buried debris is the primary challenge to effectively characterize debris within the dredging zone.
Equipment and Methods for Removal
Common attachments for debris removal include excavator buckets, thumb attachments, grapples, and clamshell buckets on excavators or cranes deployed on platform barges. Environmental buckets frequently used for mechanical dredging can remove debris materials; however, efficiency of removal will quickly diminish with increasing debris weight, size, or quantity. Hydraulic shear attachments may be used to cut root mass, logs, and trunks of trees embedded in the dredge area to minimize waste generation, maintain bank integrity, and manage the size of debris. Hydraulic dredges tend to rely more on avoidance of debris, using measures such as intake screens or pre-dredging debris removal operations. Divers can be used to facilitate debris removal and may be necessary in certain conditions; however, this approach is costly, resource-intensive, and has significant health and safety considerations. Ultimately, the equipment and attachments used will depend on the range of debris characteristics sizes, burial depths, and distribution expected to be encountered at the project site. Planning for removal operations well ahead of construction during project planning is highly encouraged such that all the necessary equipment, facilities, and material management activities can be accounted for in the contractor’s approach.
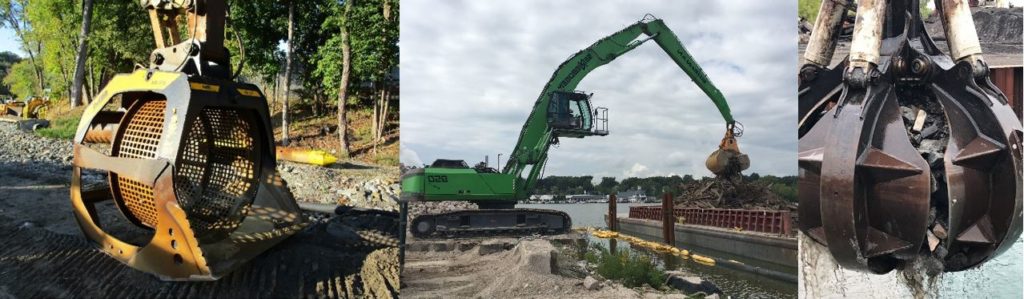
From left to right. Rotating screen for cobble materials (courtesy of Sevenson); debris scow mechanical offloading operation (courtesy of JF Brennan); grapple for debris removal operation.
In summary, existing guidance for investigations and planning for impacts of debris on environmental dredging operations have not yet been comprehensively developed, resulting in a wide range of design and construction approaches with varying degrees of risk from one project to another. A host of equipment types have been developed for debris removal and management. However, preparing remedial designs to anticipate debris issues can be challenging, especially when significant debris, most often unexpected buried debris, is discovered during construction. These difficult debris conditions may create challenges for maintaining environmental protectiveness objectives and cost-effectiveness of operations. Research is needed to understand these impacts to the 5Rs, estimate their potential costs, and develop consistent planning and best management practices. Innovations in geophysical methods and computer-aided data interpretation are needed to improve identification and characterization of buried debris. Finally, a goal of the paper is to encourage additional research and study of debris issues, including development of technical guidelines addressing debris aspects of environmental dredging.
WEDA honored “Managing Debris for Environmental Dredging Projects” with their “Why is Dredging Good” Award for outstanding paper. Upon receiving the award, the authors agreed to donate the $1,000 prize money to Water For People, a global organization dedicated to facilitating long-term access to clean water and sanitation services.
For more information on managing debris during environmental dredging operations, please contact:
Jamie Beaver, PE, Senior Engineer
734-369-3410
Contact Us
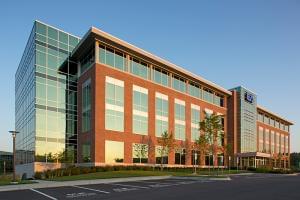